|
"It is
impossible for ideas to compete in the marketplace if no forum for
their presentation is provided or available." Thomas Mann, 1896
GETTING THE
MOST FROM MANUFACTURING CELLS
Through Focused Factory Engineering
Author: Kenneth W. Harrison
Contributed by SMW Systems, Inc.
Is Cellular Manufacturing
Reaching its Full Potential?
Most companies using cellular manufacturing have increased their productivity
and lowered their product costs. However, not all companies have achieved
extraordinary results. There are nine proven principles to gain the maximum
benefits from cellular manufacturing. Before these are covered, lets
review two definitions.
Cellular Manufacturing
In traditional factories, the equipment is arranged with similar machines
located together, i.e., all of the lathes are in one line, all of the mills are
in another line, the welders are in the weld shop and the assembly line is over
in the assembly building. With cellular manufacturing, all of the
equipment
to make a complete part is together. A cellular
manufacturing process is designed to efficiently make a specific part or a
family of parts. A typical manufacturing cell could contain the raw
material, the band saw to cut the raw material, the lathe to machine it and an
assembly/inspection bench.
Focused Factories
A focused factory unites the cells that produce the parts and subassemblies
into a cohesive unit. A large manufacturing plant that produces several types of
products could have a unique focused factory for each product line.
Focused Factory Engineering
Pumps Productivity
Changing the floor layout is not enough to dramatically reduce product costs.
The layout, product design and the manufacturing process must all change for
optimal performance. Focused Factory Engineering (FFE) is the synergism that
unites these. It typically includes the disciplines of Design Engineering,
Manufacturing Engineering, Quality Engineering, Production Planning and
Manufacturing.
Principle 1, Create Modular
Designs
The complete product must be dissected into components that can be made in a
manufacturing cell. For example a transmission manufacturer may have a
gear cell, a housing cell, a shaft cell, and an assembly cell. Whenever
possible, parts should be standardized. In this example, a standard
housing could be used to produce transmissions with a variety of gear ratios, or
a standard gear could be used in a number of different transmissions.
In order to create modules, standard interfaces must be designed. This
could mean that all gears have a 3/16" diameter hub and a 3/16"
keyway, or it could mean that transmissions are made from standard
subassemblies. A transmission with a 180:1 gear ratio could be built by
bolting four identical subassemblies together, each
with a 45:1 gear ratio.
Principle 2, Create a
Standard Process
An electro-mechanical component manufacturer was using 12
different types of solder and inspecting the process to three different
soldering specifications. This is not efficient. The process must
standardize on the fewest number of variations. Their FFE team found that
all products could be made with 3 types of solder and inspected according to one
specification. Providing a processing standard greatly increased their
manufacturing efficiency.
Principle 3, Make Similar
Components Together
I recently toured two furniture manufacturers. The recliner company
machines all chair frame parts together on the table of their vertical machining
center. After each machining cycle, a complete set of chair components is
finished. This set moves down the production line. Inventory control
is simplified because they always have the correct number of all components on
the manufacturing line, and they have found that there is nothing more efficient
than making the right parts, in the right quantities, at the right time.
The bed manufacturer, on the other hand, machines a batch of one part
then changes over and runs a batch of the next part, and so on. Not only
do they waste time because they keep changing setups, but they never have an
equal number of all required components. This method is much less
efficient than the first.
Principle 4, Schedule Special
Processes
With conventional manufacturing, a part moves from one machine in one area to
another machine in another area, and so on until the part is finished.
With cellular manufacturing, one person (or a small group of people) completes a
part in one area. The exception to this rule is when there are special
processes that require expensive capital equipment. When this is the case,
it is impractical to locate an identical piece of equipment in each cell.
Some examples are heat treating, plating, electron beam welding, and vibration
testing. When these processes can not be
eliminated they must be carefully scheduled.
Gulton-Statham is a pressure transducer manufacturer that
has a heat treatment area with two furnaces. Originally the area was
organized with a parts in rack and a parts out rack. The supervisor of the
area could not predict what parts would arrive next. Sometimes a single
part would be in process, and before it was completed, another group of parts
would arrive that needed exactly the same heat treatment profile. In order
to optimize the equipment, the company appointed one person who scheduled all
like materials on the same day. This eliminated the bottleneck and
shortened the manufacturing lead-time.
Principle 5, Eliminate
Non-value Added Time
Most manufacturing cells are not dedicated to one single
part number. A housing cell may be required to machine a dozen different
housings. In order for a focused factory to be efficient, setup changes
must be made quickly; and they should not interfere with the output of the cell.
Gregg Industries has a machine shop that specializes in machining castings.
They kit a complete setup with all the material, tooling, and inspection gages
they need to run a job. Because they have Setup SwitcherTM manual pallet changer[1] mounted on each of their vertical machining
centers, it only takes them a few minutes to change over and start machining a
new part.
Principle 6, Create a Traffic
Model for Parts
If
an assembly is missing one small part, the assembly can not ship. Imagine that
the manufacturing process is a toll road that ends in a tollbooth. The
production goals are: 1) collect the maximum number of tolls (maximize revenue),
and 2) avoid traffic over congestion because the drivers may select an alternate
route next time (satisfy the delivery commitments). If a car travels down
the entire length of road but stops before going through the toll booth, that
opportunity for revenue is lost, and it will delay the other cars attempting to
go through the toll booth.
The same thing happens with manufacturing. Any job
that is scheduled for the month, but does not ship, consumes valuable material,
labor and other resources that could have been devoted to a job that would
create revenue. In the toll road example, the greatest possible revenue can be
generated when there is a uniform and consistent flow through the tollgates.
Sometimes there are so many cars on a toll road that the
traffic jams and fewer cars are able to reach the tollbooth. It is common
for manufacturing companies to get so caught up in the daily operation (the
utilization of equipment and people) that they focus their efforts on keeping
busy and not on generating the maximum revenue. A well run focused factory
will use a production model that only allows new orders to be released at the
shipment rate, and only when all parts are available. A pull through
material handling model should be used because it minimizes the work-in-process
and efficiently moves the material through the manufacturing process.
Principle 7, Create a Plan
for Exceptions
The production line must move at a fast and efficient pace.
Exceptions such as prototypes, rework, design changes, and maintenance should
not interfere with production. If a car stalls on the toll road, it must
immediately be moved off of the roadway or the traffic flow will be affected.
The same is true of a production line.
Principle 8, Design the
Process to Include Bottlenecks
Most products only contain a few critical manufacturing
steps. These require the most expensive equipment and the most talented
operators. In a focused factory, these critical steps must be the
bottlenecks. All other steps should have built-in excess capacity.
When the capacity of the bottlenecks is known, the maximum capacity of the
focused factory will also be known. Parts should only be released into the
process at a rate that is equal to the slowest bottleneck. Releasing more
parts will only result in wasted activity, the unnecessary consumption of raw
materials, and an increase in work-in-process costs.
Principle 9, Create Standard
Documents
Some companies ask their employees to read and follow every
line of the manufacturing documentation. This is a ridiculously expensive
request. Although good documentation is important, it is a waste of time
to ask an assembly worker to read every specification or a machinist to read
every drawing note for each part. Standardization is the key to quality
and efficiency.
Manufacturing documentation should have a consistent
format. The only variation should be the process parameters that change
because of part variations. Many businesses have understood the efficiency
of using mail merge to create letters, but few have used it to create travelers.
A text template should be created that is consistent for all products that are
manufactured in a cell. Then the variable information for each part number
should be merged into the traveler template to create a unique traveler for each
part. An experienced worker will only need to scan the document for the
highlighted variables in order to have all of the information they need.
Overcoming Objections to
Change
I have heard two common reactions to these principles;
1) My company is different and . . .
2)
The principles would work if we could
start fresh, but we dont have that opportunity. Yes, every company must
find its own competitive edge. However, these principles have been used to
great advantage in some of the most efficient companies. It is true that
start-up companies do have some advantages, but they often have many more
disadvantages. Every company has the opportunity to follow the path of
continuous improvement. What each company does with that opportunity will
determine their future.
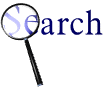 Search
Our Site
Search the ENTIRE Business
Forum site. Search includes the Business
Forum Library, The Business Forum Journal and the Calendar Pages.
Editorial Policy: Nothing you read in
The Business Forum Journal
should ever be construed to be the
opinion of, statements condoned by, or advice from,
The Business Forum Institute, its staff, workers,
officers, members, directors, sponsors or
shareholders. We pass no opinion whatsoever on the
content of what we publish, nor do we accept any
responsibility for the claims, or any of the
statements made, within anything published herein.
We merely aim to provide an academic forum and an
information sourcing vehicle for the benefit of the
business and the academic communities of the Pacific
States of America and the World. Therefore, readers
must always determine for themselves where the
statistics, comments, statements and advice that are
published herein are gained from and act, or not
act, upon such entirely and always at their own
risk. We accept absolutely no liability
whatsoever, nor take any responsibility for what
anyone does, or does not do, based upon what is
published herein, or information gained through the
use of links to other web sites included herein.
Please refer to our:
legal
disclaimer
Home
Calendar The Business Forum Journal
Features
Concept
History Library
Formats
Guest Testimonials
Client Testimonials
Search
News Wire Why Sponsor
Tell-A-Friend
Join
Experts
Contact The Business Forum
The Business Forum
Beverly
Hills, California United States of America
Email:
[email protected]
Graphics by
DawsonDesign
Webmaster:
bruceclay.com

© Copyright The Business Forum Institute - 1982 - 2013 All rights
reserved.
The Business Forum Institute is not responsible for the
content of external sites.
Read more
|
|